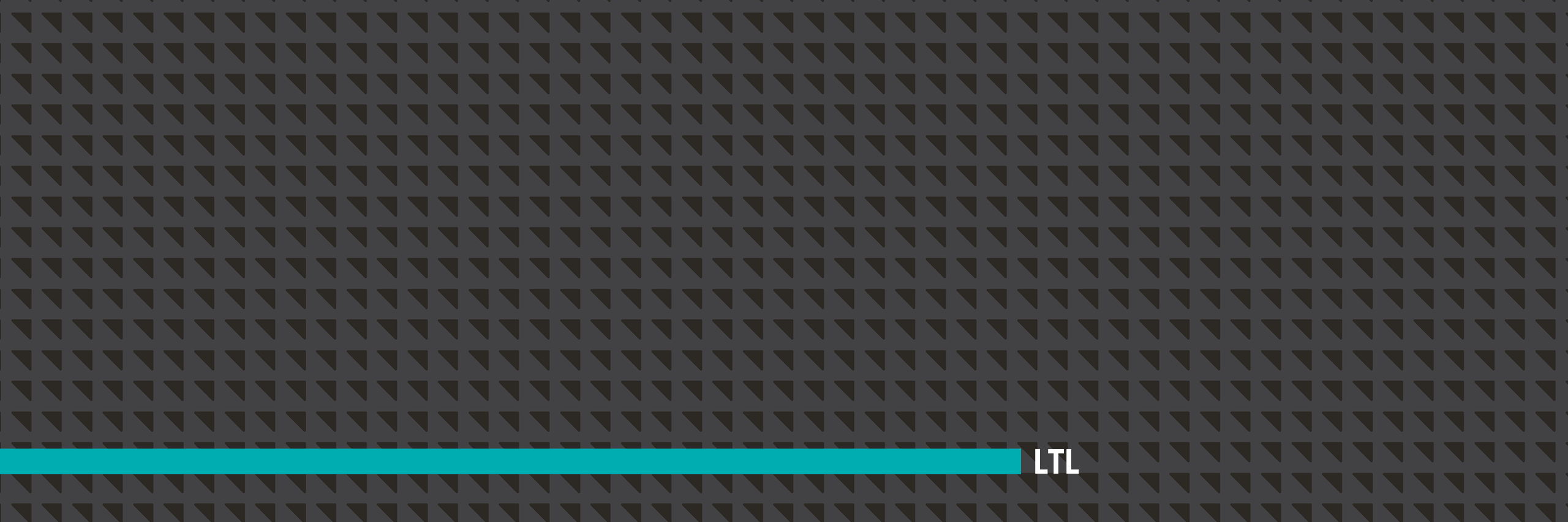
11/06/2012
Keeping it Classy: LTL Weight and Classification Tips
If you have any experience with LTL (less than truckload) shipments, you’re probably aware that it’s a complicated arena. The weight, density, class, commodity, and number of pallets all have an impact on the price of the LTL shipment, sometimes in seemingly confusing ways. It’s definitely far more complex than shipping a truckload, and there are lots of little details that, if neglected, can have a negative impact on your supply chain – and your wallet.
Many LTL carriers employ “weight & research coordinators” whose sole responsibility is to catch the “bad guys” who list an inaccurate weight or class on their bill of lading (BOL). They keep an eye out for any shipments whose description on the BOL just doesn’t seem to match up with its appearance. They will physically examine your freight, and if they deem it necessary to inspect the contents or check the weight, they’ll issue an inspection certificate… and the shipper foots the bill for the additional inspection. Even worse, if this happens to you, you’re then “flagged” as an unreliable shipper and your freight will be inspected every single time you use that carrier.
This is why it’s imperative to make sure the weight and class on your bill of lading are accurate. Don’t just guess, and don’t try to be sneaky, either! You can’t classify furniture as lumber, even though it was once lumber… (yes, believe it or not, people actually do this!) Of course, mistakes on the BOL more often come from accidental errors than they do from intentional manipulation. For example: sometimes, a shipper will routinely mark the class for a certain product as the same class it’s always been for years – but unbeknownst to them, the classification has since changed. LTL classifications can change without notice at any time! It’s hard to keep track of, but if you’re caught using the wrong class, it can mean extra charges and fees for you.
Another frequent error is forgetting to include the weight of your pallets in the total weight calculation of your shipment. For example, if you use an ERP system, you may just multiply the weight of each box and forget to consider that the pallet adds weight as well. If you forget multiple pallets, that could add up to an additional 500 pounds you’re missing. That’s not just a few pounds off. Most LTL carriers have scales installed right on their forklifts that double-check the weight listed on the BOL automatically. If there’s a significant difference, you will be charged for the extra weight… and – you guessed it – more extra fees.
Luckily, Trinity has the LTL expertise to help you circumvent these potential issues. If you work with us on your LTL shipments, while we’re ultimately not responsible for what you put on your BOL, we can help you with the process of accurately classifying your shipments and making sure everything jives. Our LTL team meets multiple times a year to go over classification changes, and if you’re a frequent customer, we can even set up an alert to let you know that the classification for your product has recently changed.
The bottom line: shipping freight LTL is complicated, but the good news is that you don’t have to do it alone. If you’re feeling overwhelmed or just plain frustrated with the process, please reach out to us and let our LTL logistics consultants help you simplify your supply chain. Hopefully, these tips will help you in the meantime!