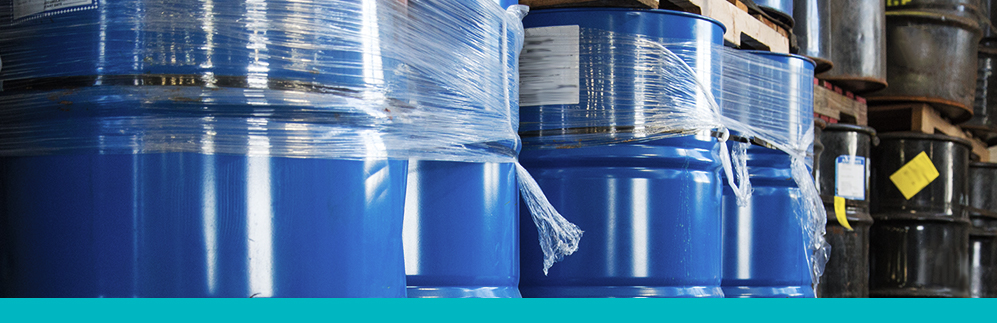
08/13/2021
Shortages are Affecting the Chemical Industry
What do semiconductors, plastics, furniture, chlorine, and more all have in common lately? They are near impossible to find. As disruption after disruption has interrupted supply chains, shortages are now messing with shipping and demand. Specifically, raw material and product shortages are affecting the chemical industry. With many other industries relying on the chemical industry, this is becoming a significant challenge to overcome.
MATERIAL AND PRODUCT SHORTAGES
Shortages in the chemical industry have worsened over the last quarter. According to a June survey of 84 National Association of Chemical Distributors, nearly 85 percent of distributors report at least one imported item as out-of-stock. This is a huge jump compared to only 47 percent found in March. Inventories in the chemical industry have begun increasing, but they have yet to reach their pre-pandemic levels. These shortages are not only hurting the chemical industries but the many industries that rely on them. One example is the shortage of citric acid, as it’s often used in vitamin or electrolyte drinks, even in soda. These material shortages mean tight supplies, high prices, and continued delivery delays.
Some recent materials and products that currently face shortages in relation to the chemical sector:
Semiconductors
Many manufacturers worldwide are having trouble securing supplies of semiconductors, delaying the production and delivery of goods, and increasing prices. Several factors are driving the crunch, which first affected the auto industry. The shortage is going from bad to worse, spreading from cars to consumer electronics. With the bulk of chip production concentrated in a handful of suppliers, analysts warn that the crunch is likely to last through the rest of 2021. Materials most vulnerable in semiconductor production include wet chemicals, solvents, photoresists, gases, and substrates. Several semiconductor process materials in the petroleum supply chain are also running short. Those materials include acetone, PGMEA, NMP, and IPA, and a few of several solvents.
Plastics
Yet another shortage complicating business is plastics. Food packaging, automotive components, clothing, medical and lab equipment, and countless other items rely on them. Since March 2020, a perfect storm of events has been putting severe strains on the supply of plastic raw materials, base plastics, and compounded plastics. This shortage has hit plastic product manufacturers very hard.
The demand for plastics continues to surge, especially for food packaging and automobile components plastics production. Plastics required by high purity chemical providers for packaging and wet processing equipment are experiencing raw material price increases due to availability issues.
Plastics make every kind of product imaginable — from food packaging, appliances, smartphones, and car parts to exercise equipment and roller skates. So with the ongoing surging demand for goods, it’s easy to see why these shortages are a big deal.
Chlorine
The swimming pool boom from the pandemic created a higher chlorine demand, thus contributing to a shortage. There was also a manufacturing lab fire in August of 2020 in Louisiana that only further aided the shortage.
Some pool supply stores have imposed quantity restrictions. In certain regions, prices for chlorine tablets have doubled from last year. The chlorine shortage is widespread, and it will likely worsen as homeowners use their swimming pools for the season.
Gas, Oil, Fuel
It’s not quite that there’s a huge shortage of crude oil or gasoline. Instead, it’s a shortage of tanker truck drivers who deliver it. According to the National Tank Truck Carriers, 20 to 25 percent of tank trucks in the fleet are parked due to the shortage of qualified drivers. The driver shortage has been an issue for a while, but the pandemic multiplied it.
Gas prices, which typically rise at the start of the summer as seasonal regulations take effect — requiring the more expensive “summer blend” of gasoline needed to combat smog — are also rising. The national average has surpassed $3 a gallon this summer and could get even higher if any hurricanes hit the Gulf Coast or if there are any other disruptions to supply, such as a refinery fire.
Other Raw Materials
As countries work to switch over to green energy, the demand for copper, lithium, nickel, cobalt, and other rare earth elements is soaring. And these raw materials are vulnerable to price volatility and shortages as limited access to known mineral deposits is another risk factor. Only three countries together control more than 75 percent of the global output of lithium, cobalt, and rare earth elements – the Democratic Republic of Congo, China, and Australia. Constraints on the supplies of their raw materials — especially polyethylene (PE), polypropylene (PP), and monoethylene (MEG) — are leading to factory shutdowns, sharp price increases, and production delays.
SHORTER SUPPLY + HIGHER DEMAND = HIGHER COSTS
Consumer spending rapidly grew because of the pandemic. Remote working and schooling created an increased demand for electronics. Higher demand came for food packaging and healthcare markets. Automotive production rebounded and surged beginning in the third quarter of 2020. All these and more are impacting the chemical industry.
These disruptions have undoubtedly led to rising prices. Echemi reported in late March that more than 20 chemical companies including BASF, DuPont, Dow, DSM, and LANXESS, have raised prices. These price hikes are largely due to difficulty in getting raw materials used to make products. And there’s less supply than there was a couple of months ago. As demand is rising relative to production, prices have increased for chemicals, like polypropylene, acetone, and other solvents.
…AND LOGISTICS DELAYS
Not only have shortages worsened since March, so have delays. NACD’s survey found that 82 percent of respondents are dealing with an average uptick in travel time for their shipment of 11 days or more. And these issues extend throughout the supply chain.
Containers and boats to ship products from overseas are in short supply. Products could be sitting in a factory overseas for months because they can’t get loaded onto a ship. Then you have the ports struggling with delays. Currently, you can look at live video outside of Los Angeles and you’ll see up to 30 boats driving around waiting to get an appointment because there are so many ships coming in. Ships are waiting longer to get in and once they do get in, there is a shortage of drayage drivers that only adds to the congestion.
A lack of truck drivers and warehouse workers has contributed to the delays as well. The driver shortage was an issue before COVID, but the recent labor shortage in warehouse workers has created a larger problem. Say you do have a truck available. But if you don’t have somebody in the warehouse to pull the goods out of the racks and load them on the truck, then that’s another issue causing delays.
Supply chain issues continue to hamper the whole of manufacturing. It’s hard to look at the global supply chain and not think, “everything that can go wrong has.” The impact of these issues continues to impact many industries downstream. On raw materials such as chemicals and plastics, inventories are unlikely to be rebuilt amid continuing strong demand. There’s simply not going to be a quick return of inventories.
WHAT YOU CAN DO DURING THESE TOUGH TIMES
Begin building a more resilient supply chain
Consider moving manufacturing operations closer to home. This can help reduce your transportation times from future delays or disruptions. Make plans now to be prepared for all potential disruptions. Disruptions to the supply chain are not new, but this current phase of repeat instances has been rougher than most.
Gain access to technology
Integrating technology into your supply chain has now become a necessity. Implementing technology like a transportation management system (TMS) will help all stakeholders maintain real-time communication and visibility. A TMS can help you optimize your routes and work with the best carriers, increasing your service levels and reducing any delays. It can provide you with data-driven insight so you can better manage current and future disruptions. And by using data analytics, you can recognize which carriers most likely have available capacity, reducing your time spent on transportation coverage. Gain insight into what’s happening across all markets, ensure proper rates for shipments, and keep more control over your budget and logistics costs with TMS technology.
Work with experts that keep a pulse on the market
An expert can help you pick up on early warning signs and help you prepare for potential constraints. They can also offer you alternative solutions when needed.
Here at Trinity, we are a Team of experts. We do more than arranging your freight. When working with Trinity, we become logistics partners in your business and aim to help you with your growth. We can help you streamline your logistics procedures and give you insight into the freight market. We keep a close eye on it and keep you educated to help you plan and forecast.
We also work very hard to follow through on what we say we are going to do. When issues arise, we work until they are resolved, keeping communication every step of the way. We have over 40 years of experience in logistics and industry challenges in supply chains is our day-to-day.
Industry experts and forecasters are saying this tough market is far from over. It may even look to extend into 2022. So don’t hesitate in asking for help. We’re here and ready to provide you with our People-Centric approach for you during this historical time in logistics.
REQUEST A QUOTEAuthor: Jennifer Braun