Stay up to date on the latest information on conditions impacting the freight market, curated by Trinity Logistics through our Freightwaves Sonar subscription.
READY FOR A REBOUND?
Given the sluggish flow of freight in 2023, seeing any signs of life is encouraging. The industry muddled through the first four months of the year with the volume index registering very little movement as seen in Figure 1.1.
Heading into late April, and the early part of May, seeing upward movement was a welcome sight to carriers and intermediaries. Mid-spring typically brings a bounce from produce and seasonal freight, and this year we are seeing that lift, albeit not at an aggressive pace. Still, even with the slight upturn, freight opportunities continue to be gobbled up by carriers, particularly on the contract side. Historic low rejection rates of under three percent not only mean less freight heading to the spot market, but shippers continue to have the pendulum in their favor with regard to rates.
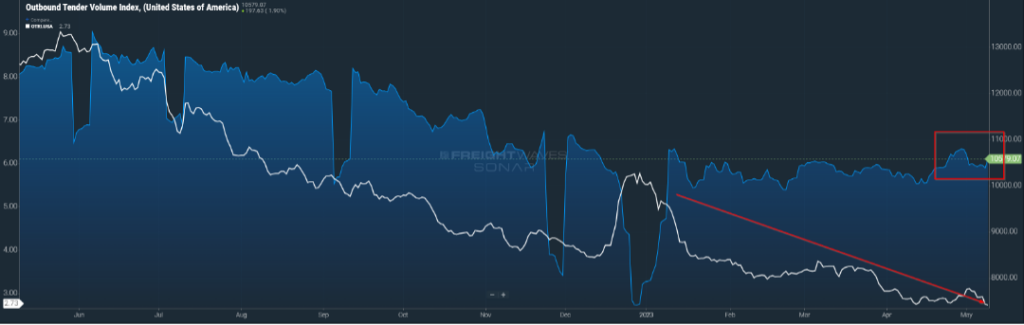
FLATBED SEES BALANCE
Speaking of tender rejection rates, the low rejection rate is not being felt across all types of equipment as we see in Figure 2.1.
Vans and reefers are pretty much accepting anything that comes their way. These are two equipment types that saw increases in their number from mid-2020 through 2022, primarily in response to the overwhelming consumer goods demand which typically travels in these types of trailers. Now that demand for these items has cooled, vans and reefers find themselves in a situation where demand is still there, just nowhere near what it was the past few years.
Flatbeds, on the other hand, did not experience the same demand. In the over-heated freight market, we experienced in the last few years, flatbeds felt the most normal with regard to freight patterns and demand. While they did not get the direct benefit of shippers clamoring for their services, flatbed carriers have also not experienced the same falling out. As a result, they enjoy a balanced market with rejection rates hovering in the mid-teens. This could be short-lived as downward trends in manufacturing and industrial production, combined with a cooling housing market, will lessen the demand for flatbed services.
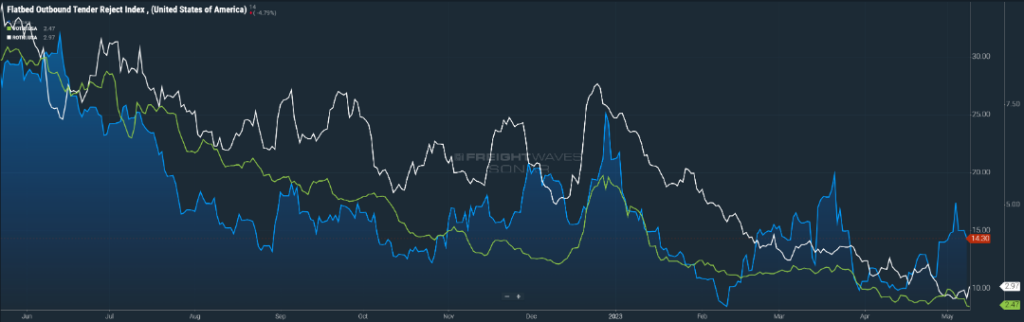
the gap remains
Carrier rates continue to normalize.
As seen in Figure 3.1, the spot rate on the van side seems to have found a bottom. Contract rates have contracted slightly, but the spread between carrier-published rates and those available with spot rate pricing continues to push past $0.70 per mile. An uptick in spot rates may relieve some of the pressure from shippers on the contracted side for carriers. Ideally, a spread of $0.15-$0.20 would be more balanced.
Could this modest uptick in volume shrink the rate gap even more? Stay tuned to June’s update to find out.
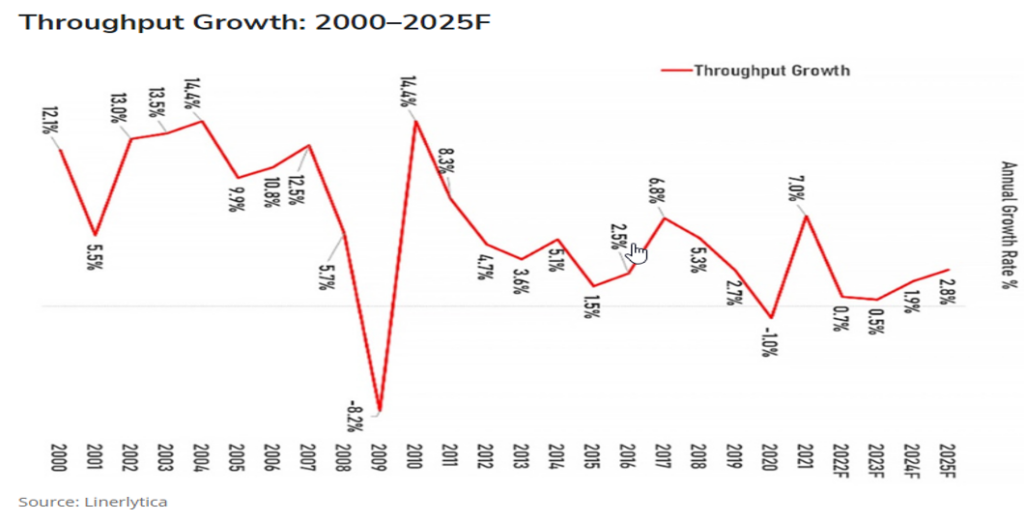
Stay Up To dAte
Looking for a more frequent update? Subscribe to our newsletter and receive Weekly News Updates every Friday by selecting “Weekly News Update” when you select your preferences.
Join Our Mailing List for Frequent News UpdatesTrinity Logistics is proud to announce its recognition as a Top Freight Broker by Transport Topics for the 21st consecutive year, ranked 17. This honor serves as a testament to the company’s continued commitment to delivering outstanding People-Centric service in the logistics industry.
Transport Topics is a leading publication in the transportation business and is well-known for its annual comprehensive rankings of freight brokerage firms. Companies are ranked based on gross revenue and services offered.
Trinity Logistics is thrilled to have made spot #17 on the Top Freight Brokers List for 2023 as this accolade reflects Trinity’s commitment to delivering exceptional service to customers and helping them meet their unique logistics needs. With a core focus on exceeding expectations, the company has built a reputation for its integrity, reliability, and customer service.
“This recognition continues to showcase our ability to serve our shippers and carriers with People-Centric Freight Solutions®,” says Sarah Ruffcorn, President of Trinity Logistics. “Team Trinity works hard to continually strengthen our shipper and carrier relationships, providing value to them in simplifying their processes and providing an excellent Trinity experience. Earning this recognition continues to show we are rising to the ongoing supply chain challenges and are serving our customers well. Thank you, Transport Topics, for the recognition. We’re honored to have made it another year in the top 20’s – #17!”
Trinity’s parent company, Burris Logistics, has ranked number 35 on Transport Topics’ Top 100 Logistics Companies List and number 4 on their Top Refrigerated Warehousing List.
To see the complete list, visit Transport Topics.
About Trinity Logistics
Trinity Logistics is a Burris Logistics Company, offering People-Centric Freight Solutions®. Our mission is to deliver creative logistics solutions through a mix of human ingenuity and innovative technology, enriching the lives of those we serve.
For the past 40 years, we’ve been arranging freight for businesses of all sizes in truckload, less-than-truckload (LTL), warehousing, intermodal, drayage, expedited, international, and technology solutions.
We are currently recognized as a Top 3PL and Cold Storage Provider by Food Logistics, a Top Freight Brokerage Firm by Transport Topics, and as an Inbound Logistics Top 100 3PL.
Work with a Top 3PL – Get a Freight QuoteStay up to date on the latest information on conditions impacting the freight market, curated by Trinity Logistics through our Freightwaves Sonar subscription.
SIMPLE SUPPLY AND DEMAND
We probably all remember at some point in either our high school or college career hearing about supply and demand. A pretty simple concept that applies to goods, commodities, services, and yes, transportation. A great indicator of that is shown in Figure 1.1 which shows the growth in for-hire carriers (blue line) and the outbound tender volume index (green) since mid-2018. While this is not a 1:1 comparison, it clearly shows, especially in the past three years, how supply and demand have been the driver of transportation costs.
From roughly mid-2020 until the early part of 2022, demand was high compared to prior years, and the supply side (carriers) was trying to catch up. As a result, carriers were able to dictate rates in the market. As the supply side began to accelerate, the over-heated freight market began to normalize in late 2021/early 2022, retreating to levels seen prior to the pandemic. The rate pendulum once again swings to the shipper’s side. Some have argued based on this over-capacity situation that it could take years before there is once again equilibrium. Agree, it will take, unfortunately, attrition on the carrier side, combined with a rebound on the freight activity side to find that balance. However, taking years to do so is a bit aggressive. Most likely, mid-2024 will see supply and demand as it relates to transportation reaching a better balance.
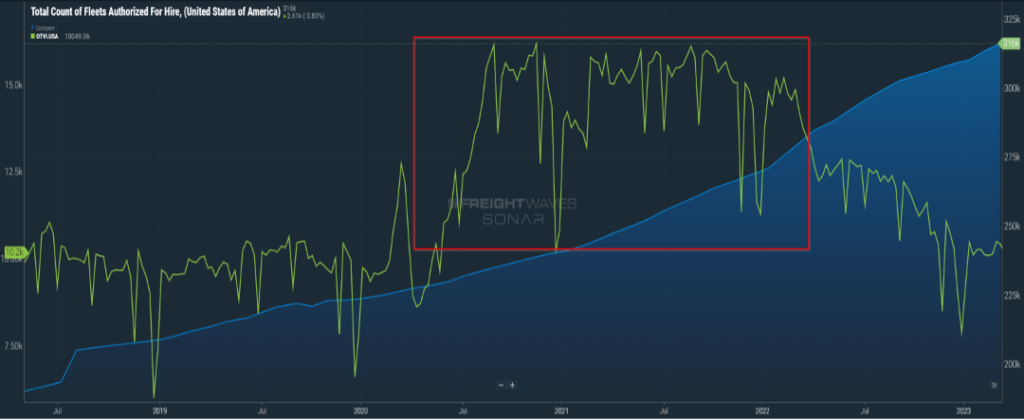
THE GAP
We looked at this last month, but the lag between spot and contract rates remains at historic levels. Typically, you will see a gap of maybe 10 cents or 15 cents per mile, but for the last five months, that gap has remained above the $0.50 per mile mark, currently trending at $0.86 per mile higher on the contract versus the spot side.
As you can see in Figure 1.2, that increase in the contract-to-spot gap has been in lockstep with the decreasing outbound tender rejection rate. As carriers with contract pricing are finding fewer freight opportunities versus 2021 and 2022, they are taking almost every shipment tendered their way. On average, for every 100 contracted shipments tendered to carriers, they accept 97 of those shipments. For shippers, it will be a balance between finding cost savings with spot capacity and fulfilling the requirements they have with higher-priced contracted carriers.

BLAH IMPORT CONDITIONS
On the international side, particularly imports, we continue to see declining volumes and blank sailings. While the ports were inundated in late 2020 through the first half of 2022, that volume has stalled. Stalled to the point where the largest U.S. port of LA/LB encountered almost 100 ships at one point waiting to offload to now having “plenty of good parking spots available.”
Figure 1.3 clearly demonstrates the decline in consumer demand, along with near-shoring efforts, and the year-over-year impact. Expect, for lack of a better word, blah import conditions throughout 2023 with a rebound on the horizon for ’24 and ’25.
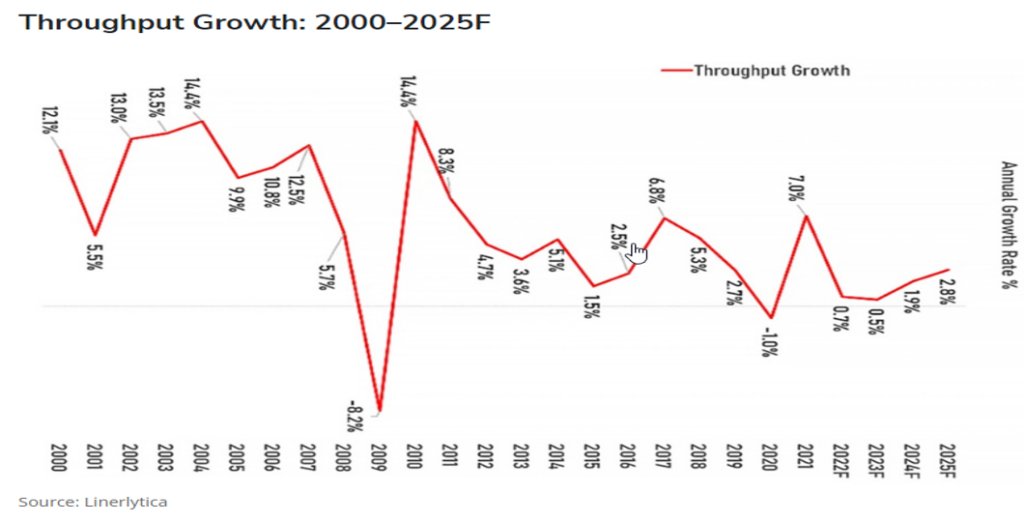
Stay Up To dAte
Looking for a more frequent update? Subscribe to our newsletter and receive Weekly News Updates every Friday by selecting “Weekly News Update” when you select your preferences.
Join Our Mailing List for Frequent News UpdatesStay up to date on the latest information on conditions impacting the freight market, curated by Trinity Logistics through our Freightwaves Sonar subscription.
WHEN WILL FREIGHT VOLUMES START TO IMPROVE?
That is the $64,000 question. Since the start of the year, freight volumes have been stable but certainly suppressed as compared to the last few years (Figure 1.1). In addition, the rate at which carriers reject shipment tenders is almost nil, with almost 97 percent of the freight tenders being nabbed by carriers with contract pricing.
We will certainly see the seasonal freight patterns in 2023, with produce and outdoor products providing a boost in the coming weeks. And the end-of-year push for back-to-school and Christmas should also lend a boost, although that end-of-year buying seems to be more spread throughout the year. Many in the industry got accustomed to an over-heated, reactionary market over the past few years. With that as the backdrop, the one word I can think of to describe how the market will feel is “blah” in 2023.
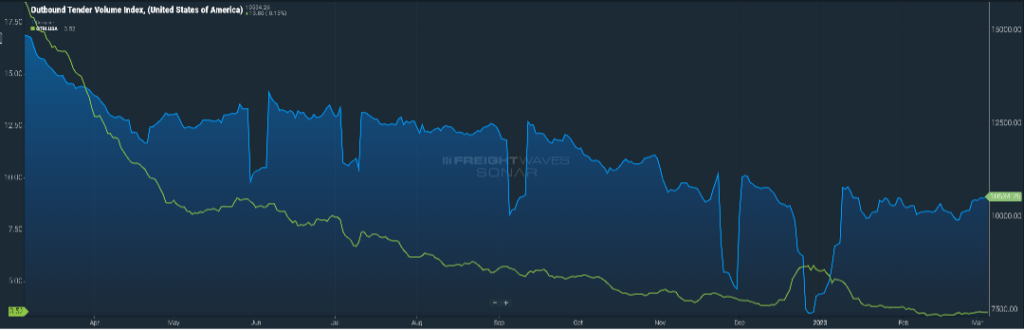
Contract rates continue to outpace the spot market. While carriers with submitted contract rates are right-sizing rates in response to the market, expenses that have been exaggerated over the past few years, such as driver pay and benefits, maintenance costs, and insurance premiums, are keeping contract rates well above spot.
As one can see in Figure 1.2, as rejection rates have declined, meaning less freight being pushed to the spot market, it has a mirror effect on the spread between contract and spot rates, currently sitting at $0.84 less per mile on the spot side. Shippers will continue to fulfill their contractual obligations with regards to tendered volume, but being able to utilize the spot market does bring cost savings to shippers.
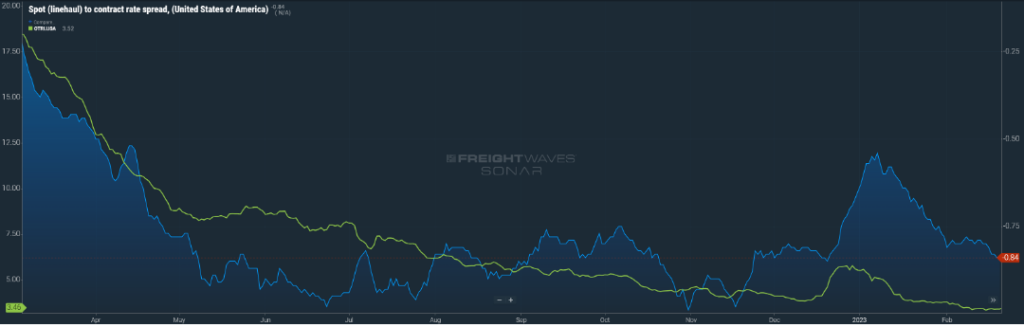
Finally, activity at the ports continues to decline, especially on the import side. As seen in Figure 1.3, just a year ago, ports were handling 10-20 percent more inbound volume, that change today is a decrease from a year ago. Inventories have been replenished over the past year and a half, and consumer demand for goods is less. This trend is most likely to continue through the year, driving the spot container cost down and subduing activity around U.S. ports.
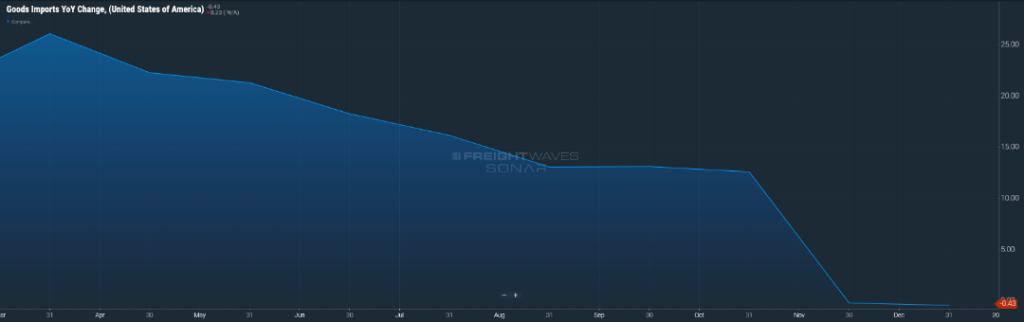
Stay Up To dAte
Looking for a more frequent update? Subscribe to our newsletter and receive Weekly News Updates every Friday by selecting “Weekly News Update” when you select your preferences.
Join Our Mailing List for Frequent News UpdatesStay up to date on the latest information on conditions impacting the freight market, curated by Trinity Logistics through our Freightwaves Sonar subscription.
SOMEWHAT HO-HUM
The current landscape for over-the-road freight looks like what it was a month ago. Freight volumes are lower year-over-year (YoY) but seem to have found a floor.
If anything, the flat lining of volume (Figure 1.1) we are seeing is eerily like what we saw in the early part of 2020. And that is not just relative to freight volumes.
Back in ’20, carriers were snatching up tenders as soon as they were offered, with rejection levels hovering in the five percent range. Right now, we are just below that five percent mark. It’s anticipated that freight flows will follow their seasonal patterns, albeit at reduced volumes compared to what we saw in 2021 and most of 2022. Spot rates continue to trend lower than contract rates, although that gap continues to shrink. It’s also anticipated that contract rates will continue to slide while spot rates should be pretty near their floor.
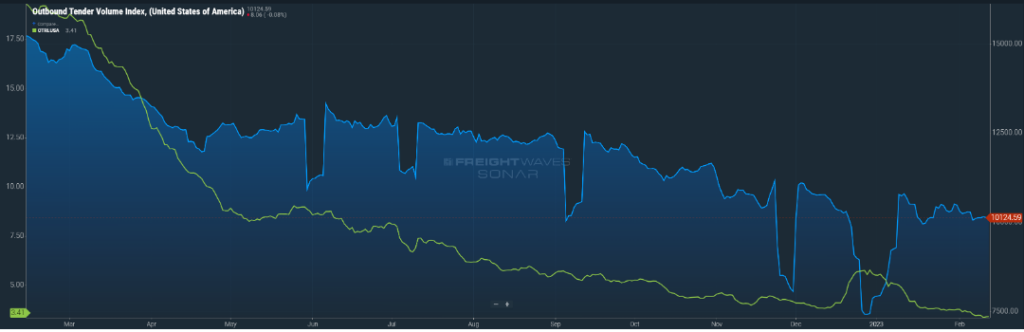
DECLINING PORT ACTIVITY
Imports will continue to weaken over the next several months. While some ports have seen slight increases in YoY volume, that increase is not indicative of an overall volume surge. It’s due to the shifting of where the freight is entering the U.S.
So, while ports like Houston (up 5.2 percent) and Baltimore (up four percent) are robust with above-average activity, major entry points like Los Angeles (down 30 percent), Oakland (down 58 percent) and Seattle (down 41 percent) are feeling the lack of volume. An opportunity should be seen with export activity (Figure 1.2). While the U.S. dollar losing value is not good for imports, it has the opposite effect on export activity.
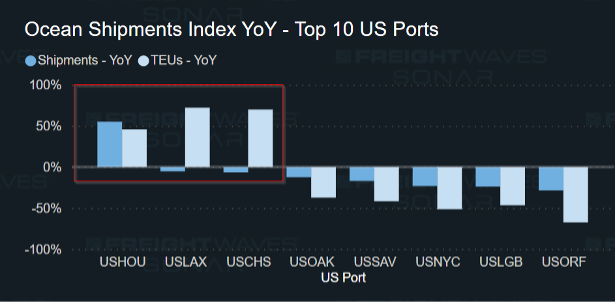
Stay Up To dAte
Looking for a more frequent update? Subscribe to our newsletter and receive Weekly News Updates every Friday by selecting “Weekly News Update” when you select your preferences.
Join Our Mailing List for Frequent News UpdatesStay up to date on the latest information on conditions impacting the freight market, curated by Trinity Logistics through our Freightwaves Sonar subscription.
Not Interested in Reading? Check Out Our Video Instead!
2023 Crystal Ball
It’s usually this time of year when predictions for the upcoming year start to make headlines. It’s safe to say that most folks could make some predictions based on what has transpired recently, so I wanted to highlight a few of those as we kick off the new year.
The gap between spot and contract rates will stabilize.
Now, this does not mean that they will be equal – that rarely happens. Just about a month ago, the spread was quickly approaching $1.00 per mile between contract and spot rates (with contract being higher). That gap is slowly starting to shrink (Figure 1.1). Some of that is due to spot rates seeing a holiday bump, and part of that is related to new contract rates taking hold. With many carriers taking an extended break from the road since mid-December, less capacity has pushed spot rates higher. This upward trend will be short-lived and expect rates below $2.00 per mile to become the norm as we chug through winter and into early spring. Contract rates will also trend downward, finding a floor most likely in the middle part of the year.

Few sectors will see bright spots in 2023.
I don’t think anyone thought the economy could continue to chug along at its rapid pace seen in the latter half of 2020 and through most of 2021. Even though 2022’s growth was not as robust as the prior year, the U.S. Gross Domestic Product (GDP) should seek out a modest two percent growth rate. However, where that growth occurred sets the stage for this year.
2022 saw a return of spending on services versus goods. So, while things like healthcare are important to the overall economy, from a freight standpoint, service spending has much less impact on transportation. Expect auto sales, both new and used, to continue their strong run. As parts and inventory issues continue to be resolved, vehicles with temporary tags will be more commonplace as Americans continue to purchase cars and trucks.
On the opposite end, most notably, the housing market will have a rough 2023. With Americans seeing inflation compete for more of their take-home dollars, and the cost of borrowing increasing, many will choose to remain in their current situation. And it’s not just the building materials that will see less of a demand. With fewer new homes comes less demand for things that go in those homes – like appliances, carpets, and furniture.
Following the building industry, manufacturing will be the next downstream effect, and banking will also see less demand for consumer and business loans. Overall, expect 2023 to see, at best, no year-over-year (YoY) growth in GDP, with 2024 being a rebound year (Figure 2.1)

Import activity will continue to slow.
As we saw in last month’s update, Figure 3.1 shows the impact of the ship backlog being resolved and container movement starting to slow. That will be a common theme this year. While 2022 saw year-over-year import activity down almost 20 percent, that downward YoY story will continue in 2023. This will have an immediate impact on intermodal activity, but also over-the-road and less-than-truckload volumes will feel the impact.
One thing to keep in mind as we see recent actual and forecasted numbers showing negative, that is against a backdrop of a very successful 2021 and modest growth year in 2022. So while 2023 will not continue that positive trend, by comparison to a recent down year like 2019, 2023 will be up from an overall volume standpoint versus just a few years ago.
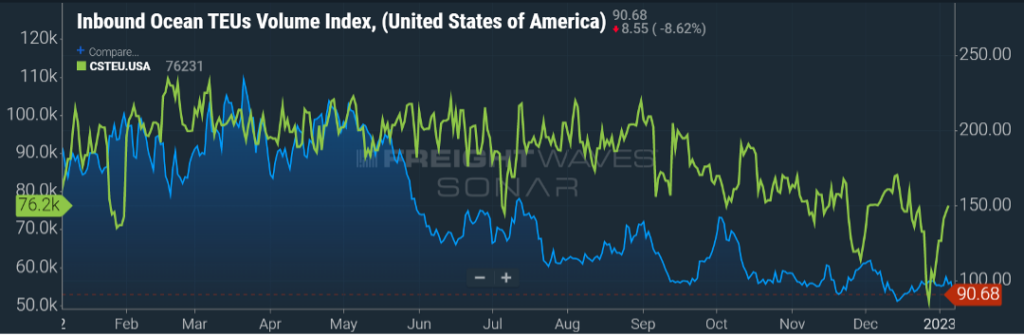
Stay Up To dAte
Looking for a more frequent update? Subscribe to our newsletter and receive Weekly News Updates every Friday by selecting “Weekly News Update” when you select your preferences.
Join Our Mailing List for Frequent News UpdatesStay up to date on the latest information on conditions impacting the freight market, curated by Trinity Logistics through our Freightwaves Sonar subscription.
As we near the end of 2022 and the start of 2023, let’s look at three things in relation to the freight market: freight volumes, the rates, and what’s happening in the maritime segment.
SLOWING FREIGHT VOLUMES
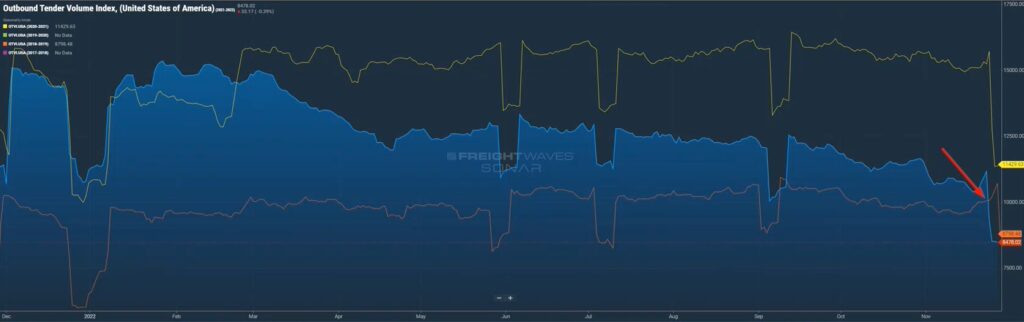
In Figure 1.1, you can see the contracted outbound tender volume index over the past four years. The yellow line on the top represents 2021, the blue line represents 2022.
Since about the end of the first quarter of this year, we started seeing those volumes pacing around the same way as last year, but then all of the sudden they started to take a nosedive. Contract volumes are down around 15 percent below 2021 levels. What that means is we’re seeing less volume trickling to the spot market and this trend will certainly continue as we go into 2023.
FALLING RATES
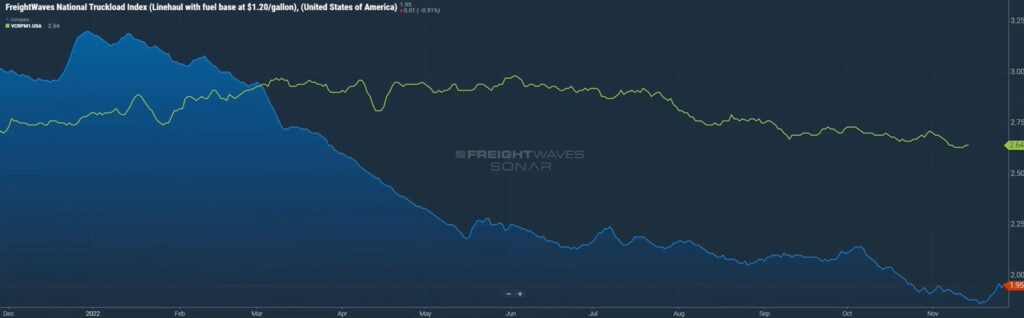
Speaking of rates, in figure 2.1, you’ll see the top green line represents the average van rate for contracted freight. The blue line is vans for the spot market.
As you can see, just like with freight volumes, they were running neck and neck until about March, and then there was a discrepancy. We’re seeing this on the rates side as well. Typically, the difference between contracted and spot rates is maybe 10 or 15 cents per mile. The fact that right now it’s about 70 to 80 cents a mile, we’ve never seen it at that high of a discrepancy. We do feel that as we get into the bidding season, new contracted rates will start to kick in, so we do anticipate that the green line will trend down. I’m not sure how much the blue line, the spot line, can continue to go, as it’s currently sitting at just below $2.00/mile. We may soon reach a point where carriers are not profitable on spot rates.
FINDING MARITIME BALANCE
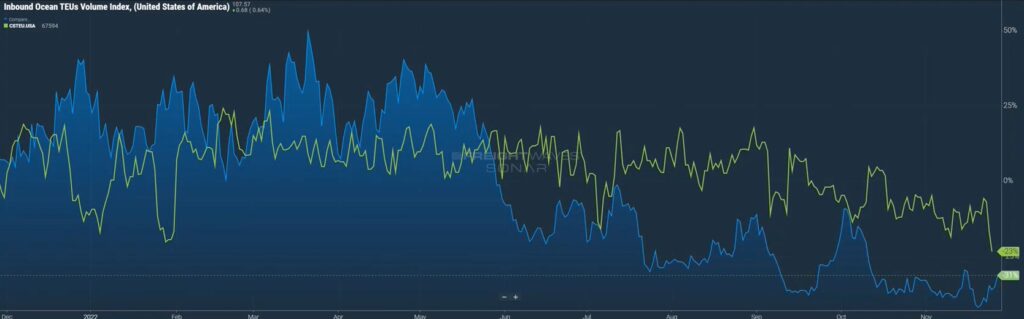
On the maritime side of things, in figure 3.1, the green line shows the number of actual containers that are clearing customs. They are coming off the ships, being unloaded, and clearing customs to be distributed via warehouses, intermodal, truckload, and what have you. The blue line shows the number of actual import bookings that have happened.
You may say to yourself, that doesn’t make sense. If somebody is booking freight and that number is going down, how come we are still clearing these containers? Remember, throughout much of 2021 and even 2020, there was a backlog of ships, particularly on the West Coast, waiting to get unloaded. So, while the flow of ships is not coming into the ports as greatly as it was, it just kind of shows you how big of a backlog there was, that it’s taken six months and we’re still not through this backlog of ships, both on the West and East Coast.
Overall import volume is down 20 percent year over year. Yet, East Coast and Gulf ports are up as shippers moved their freight to the East Coast when the West Coast was originally facing backlog delays.
KEY TAKEAWAYS
Low, single-digit rejection rates on contracted freight mean less is hitting the spot market, by some accounts 30 percent less than last year.
Carriers need, and we need carriers, to remain solvent. Be diligent in negotiations with carriers but understand that we are very close to the floor for when a carrier becomes unprofitable.
Less freight is coming through the ports. Short-term will trigger an over-supply situation, particularly on ports with declining YoY volumes like Los Angeles and Long Beach. Other ports like Savannah, Houston, New York, and New Jersey will see more capacity balance.
Stay Up To dAte
Looking for a more frequent update? Subscribe to our newsletter and receive Weekly News Updates every Friday by selecting “Weekly News Update” when you select your preferences.
Join Our Mailing List for Frequent News UpdatesIt’s no surprise that one of the hottest topics in the world lately is the pain felt at the pump. Rising fuel prices have been at an all-time high, surpassing the costs since 2008, and these prices will only continue to climb. As a result, businesses are being forced to pay more to operate, causing a ripple effect for everyone.
Wait, How Did This Even Start?
You may be wondering how fuel prices even got to this all-time high. Well, they can’t be blamed on any specific event or occurrence as many different factors caused fuel prices to surge.
World Conflict
World conflict is one issue affecting fuel prices, specifically those in Western Europe. The Russia-Ukraine war has been brewing for some time now, and due to attacks, the United States among others has stopped imports, like oil, coming from Russia.
Russia is one of the world’s largest oil exporters, exporting nearly eight million barrels in one month. The drastic change in accepting oil imports from Russia has caused the price of fuel to rise because it’s not as available as it once was.
The Dreaded “C” Word
Another catalyst for the spike in fuel prices is the continual effect of Covid-19. I’m sure you’re tired of hearing it, but the world is still feeling the pains of the virus while we aim to return to life. Recently, Covid forced Chinese ports to close for a brief period and now that the ports are opening back up, supply cannot keep up with demand.
As people try to live alongside Covid-19, office workers are going back to in-person work and people are returning to travel after two years of staying put. With more people leaving their homes, it’s causing a greater demand for fuel while our supply is limited.
The Effects of These Issues
Fuel prices are affecting everyone, including consumers, and businesses, but those in the logistics industry are seeing greater challenges. That’s because the logistics sector has seen disruption after disruption. First, with the issues started by the pandemic, then the port congestion once businesses began to reopen, and so on to now with increased fuel prices. This industry has barely had a moment to catch its breath.
Logistics is at a crossroads; with the United States economy looking at a recession, and world conflicts yet to improve, it’s going to be hard for fuel prices to drop back to normal levels until everything balances out.
How Bad is it Actually?
Even though everyone has been hearing and seeing the high fuel prices, how bad are these prices? Well, in June, the U.S. national average price per gallon topped $5, which is 50 percent higher than it was this time last year. Even pre-pandemic prices were at $2.55 average for that month, showing the direct impact that covid and other issues have caused.
These prices only continue to rise when we talk about the cost of diesel fuel. This type is often more expensive than regular gas, and this is what truck drivers use to fill up their tanks. In June, diesel fuel averaged $5.50 per gallon in the U.S., which is a .50-cent increase from regular fuel. While this increase seems small, when truckers are driving over 500 miles per day, the extra cost can add up quickly.
President Joe Biden has tried to take steps to lower fuel prices in the United States. He has called on Congress to do a Federal Gas Tax Holiday, releasing the charges that the federal government has on fuel. Typically, the government charges an 18-cent tax per gallon on gasoline and a 24-cent tax per gallon on diesel, but President Biden has called for the Tax Holiday to give Americans breathing room as they battle other economic issues like inflation.
High fuel prices are not an issue solely faced by the United States. In fact, gas prices in the United States are on the lower end of the spectrum compared to other countries. For example, while the average in June for the United States was $5 per gallon, in Germany, it averaged $8.26 per liter, while one of the highest fuel prices was in Hong Kong, where gas was $10.71 per liter in June.
How Do High Fuel Prices Impact You?
So, how do the rising fuel prices affect those in the logistics industry? Well, let’s take a look.
Shippers
Increased fuel prices mean higher logistics costs because it’s now more expensive to move their products from point A to point B.
Consumers
Consumers see a direct cost increase on products due to fuel prices. Because it now costs more for shippers to move their products to their destinations, they must also raise the price of their products to continue to make a profit.
Carriers
The biggest issue carriers are seeing with the high fuel prices is the impact on their income. Their operating costs have increased due to the rising fuel and product prices. And with rates lower than they’ve been throughout the pandemic, many carriers have decided to put a pause on driving until the market return to normal. This could cause added chaos to the market. Should more carriers halt their work, there could be an imbalance in the industry, causing more backlogs and shipping delays as a result.
Trinity is Here to Help
As an experienced third-party logistics company with over 40 years in business, we’ve worked with many shippers and motor carriers through the ups and downs faced in this industry, including this one. We’ve seen it all and are here to help you through these troubling times.
Whether you’re a shipper looking for better logistics management or a motor carrier looking for dedicated freight to keep you consistently moving, you can find all the solutions you need with our People-Centric approach.
Get connected with us today so you can start having Trinity Logistics, a Burris Logistics Company, by your side, no matter the state of the market.
Learn more about Trinity Logistics Join our mailing listIf you follow any of the transportation or trucking-related publications or are situated on the West Coast, you probably have seen or heard the term “AB5”. The AB5 law, popularly known as the “gig worker bill”, is formerly known as California Assembly Bill 5. Here’s a quick rundown of how it came to be, what it means, and who is affected.
WHAT IS THE AB5 LAW TIMELINE?
- Passed by the California Senate and House, and signed into law by the Governor of California in September 2019
- A preliminary injunction delayed the enactment of the bill in 2020
- In June 2022, the Supreme Court of the U.S. declined to hear the appeal, thus rendering the injunction defunct and AB5 cleared to be enacted
WHAT DOES THE AB5 LAW MEAN?
At its core, the bill was passed to decide if a worker meets the classification of an employee or maintains independent contractor status. The bill uses a three-prong test to determine a worker’s classification. To be identified as an independent contractor, a worker must:
- Be free from the control and direction of the hiring entity in connection with the performance of the work, both under the contract for the performance of the work and in fact.
- Perform work that is outside the usual course of the hiring entity’s business.
- Be customarily engaged in an independently established trade, occupation, or business of the same nature as that involved in the work performed.
WHO GETS AFFECTED?
Like any piece of legislation, there are exceptions. Unfortunately, independent contractor truck drivers, otherwise known as owner-operators are not part of the exception list, and that number is approximately 70,000 in the state of California. Trucking companies that utilize the service of owner-operators to run their business are at risk of being in violation of the law.
IF I WANT TO WORK WITH A motor CARRIER BASED IN CALIFORNIA, DO I NEED TO VERIFY THAT THEY ARE AB5 COMPLIANT?
As with any carrier, whether they are based in California or any other state, they are required to comply with all federal and state regulations. Some states have more regulations than others, with the California CARB regulation being a good example. As with those regulations, the responsibility to comply 100 percent lies with the carrier.
WHAT COULD BE THE IMPACT OF THIS LEGISLATION TAKING EFFECT?
The estimate is that 70,000 truck drivers in the state of California could be impacted. Certainly, there is the option for companies that utilize these independent truck drivers to hire them as employees. That may be unlikely as these drivers enjoy the benefits of running their own business versus being a company driver. There is also the possibility that owner-operators will look to relocate outside the state of California. Nonetheless, this law will put further pressure on California’s capacity among current activity in ad around California’s ports, creating another disruption to the U.S.’s already stressed supply chains.
STAY UP TO DATE
Subscribe to our newsletter and receive Weekly News Updates every Friday by selecting “Weekly News Updates” when you select your preferences.
Join Our Mailing ListHow do we get supply chains back on track after years of constant disruption and setbacks? The supply chain backlogs came largely from the shock at the start of the pandemic, but even before then, there have been many supply chain vulnerabilities.
Supply Chain Resiliency: Alleviating Backlogs and Strengthening Long-Term Security
Recently, Congress met to discuss our national and global supply chains, current supply chain issues that we need to focus on now, and how to build supply chain resiliency for the long term. Congress invited individuals and organizations to come to testify, to present their views for inclusion on the topic. U.S. Senator for Delaware, Tom Carper, asked Doug Potvin, Chief Financial Officer (CFO) of Trinity Logistics to testify.
With 16 years of service at Trinity and over 30 years of industry experience, Doug sees first-hand the problems plaguing supply chains. Doug’s testimony gave the Members of this panel valuable insight into the continued problems in supply chains and how members of the Transportation Intermediary Association (TIA), like Trinity Logistics, continue to serve the nation amidst these difficult times.
Doug’s Testimony Before Congress
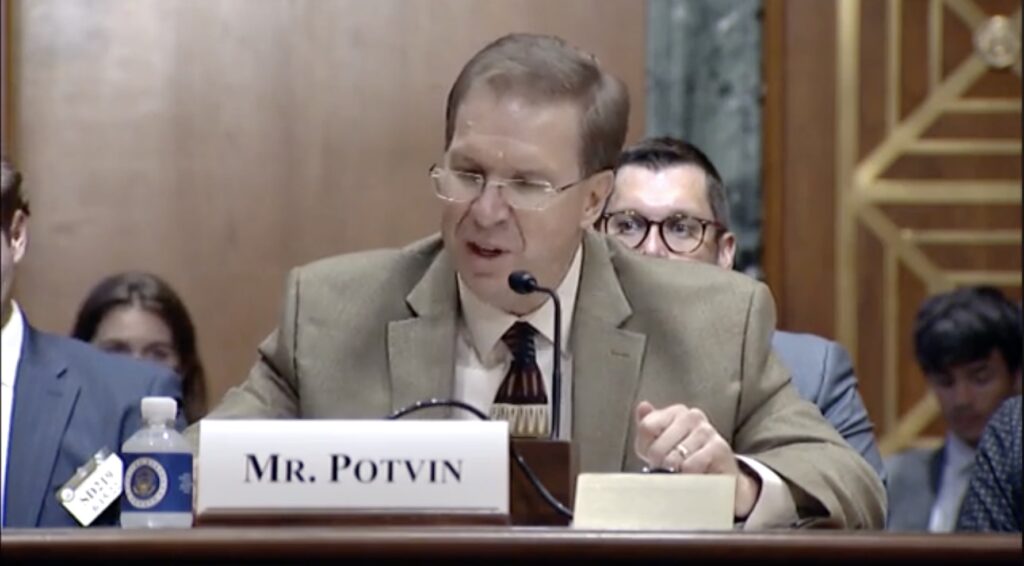
“ I want to introduce myself as the CFO, Chief Fun Officer at Trinity Logistics because we like to have fun when we’re working hard. Thank you for the opportunity to speak with you today regarding how policymakers and business leaders are addressing the existing backlogs in the supply chain in the short term and building more resilient supply chains in the long term. My name is Doug Potvin. I’m the CFO of Trinity, a third-party logistics company (3PL) headquartered in Seaford. I’m privileged, honored, and humbled here today representing Trinity, our association, Transportation Intermediary Association, and the entire third-party logistics industry that we serve.
We serve as an intermediary in solving the logistical needs of our shipper customers by sourcing capacity from motor carriers and vendor partners. We are proud to report today that this past year we’ve generated over 1 billion dollars in revenue, arranged over half a million shipments, and offered 350 individuals full and part-time jobs. We truly are a proud Delaware company.
From Charles Dickens, the novel, The Tale of Two Cities; It was the best of times, it was the worst of times. Season of light is the season of darkness, a spring of hope is a winter of despair. Over the last two years, the same could be said of the international supply chain and from our perspective, closer to home, the domestic transportation industry.
In March of 2020 as both domestic and international countries shut our businesses including the shutting of the port cities and operations in China and the fact most consumers were at home facing an uncertain future, freight volumes plummeted. Motor carrier capacity increased dramatically due to the steep drop in goods moving and the transportation market saw prices for motor carriers fall. In fact, Trinity Logistics was mentioned on a Facebook post that we were earning an average gross margin of 60 percent, which was simply wrong.
In addition, a small number of motor carriers came to Washington D.C. and demanded rate transparency. Interesting after the businesses, ports, and countries opened up freight volumes began to skyrocket, available motor carrier capacity tightened up, and rates paid to motor carriers increased due to reflecting the change in market conditions. Demand for rate transparency went silent.
The pricing in our industry is driven by market conditions, supply and demand. Large scale, no entity on either side of the equation has enough market share to drive rates. In addition, each shipment has its own variable considerations to take into account including everything from available to capacity in various regional markets, lead time for products, dwell time at shippers and consignees, commodities needing move, and type of equipment needed. All this happens in real-time to ensure goods get to market, keeping our economy moving forward.
Now more than ever, the role of third-party logistics professionals has become more valuable. Companies like Trinity and the other 28,000 licensed property brokers are working overtime to ensure that essential goods continue to be delivered in an efficient manner to meet our customer and consumer needs. Our industry along with motor carriers are the main component as the why during the crisis and disruption, the supply chain bent but never broke.
Trinity Logistics applauds the U.S. Senate and House of Representatives’ Bipartisan passage of the Infrastructure Investment and Job Act, a historic investment into transportation and infrastructure. We’re very pleased to see how quickly the Federal Motor Carrier Safety Administration (FMSCA) established the Safe Driver Apprenticeship Pilot Program. Trinity hopes this three-year pilot program will be successful and made permanent so individuals ages 18 to 20 will explore interstate transport careers. Trinity also believes that as the spending on the Investment Act ramps up in the near future it will provide enough support to the economy to keep the motor carriers employed as we are starting to see freight volumes pull back over the last 30 to 60 days.
Trinity would also like to thank Chairman Carper, John Cornyn, Senator Menendez, and Senator Tim Scott for the support in offering legislation and getting the Senate to act unanimously in passing the Custom Trade Partnership Against Terrorism Act (CTPAT).
Currently, the vaccine mandate for truck drivers coming to the country to deliver freight from Canada and Mexico continues, these professional drivers spend most of their professional time alone in the truck cab, presenting a zero percent risk of spreading Covid-19. This should be lifted immediately to open up capacity and shorten the amount of time it takes to move goods across borders.
Another issue that greatly impacts not only the efficient movement of goods, but highway safety, is the lack of a federal motor carrier safety selection standard. Currently, because of broken safety rating systems from the FMCSA, almost 90 percent of trucking companies are considered unrated. There are no requirements in place before selecting a trucking company, that drastically impacts the overall safety of our nation’s highways. The latest report from the national highway traffic safety administration noted that the number of accidents involving commercial motor vehicles increased 13 percent in 2021. The status quo is not working, and highway safety needs to be improved. Trinity Logistics and our trade association, TIA, fully support legislation to create a motor carrier safety selection and mend the safety rating process.
The U.S. trucking spot market conditions have reflected towards weaker and more normal conditions, though we still will see what the future holds and how that trend continues. Hopefully as a result of this meeting and coordinated actions taken by the United States, our trading partners, manufacturers, supply chain vendors, our nations become resilient when facing similar conditions and uncertainty.”
Trinity Logistics would like to thank Chairman Tom Carper and the TIA for inviting Doug to testify before the Committee. He is a very valuable leader in the industry and Trinity Logistics appreciates all he does for our company, our industry, and our nation.
If you would like to watch the full hearing:
Stay in the know. Join our mailing list.